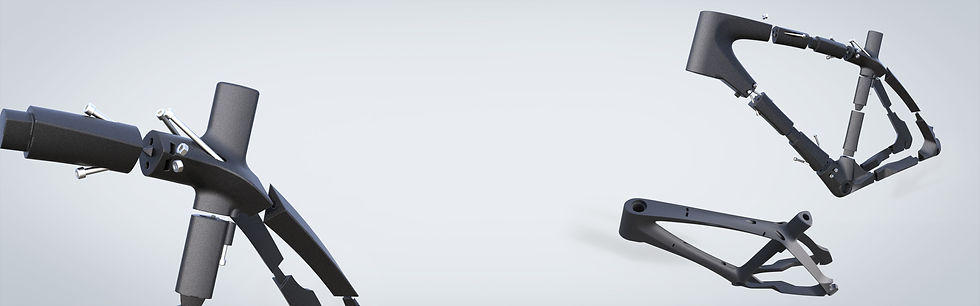
MODU
A 3D printed modular bike
Project rIDe was my studio project in spring 2016, proudly accomplished with sponsorship from Eastman Innovation Lab. Many thanks to Prof. Kevin Shankwiler and my teammates Moises Araya and Achuyth Kumar.
Since fall 2016, I've been continuing on this project as an independent study after Prof. Kevin Shankwiler to finish printing and assembling of the bike.

Video Editing: Matthew Gregory
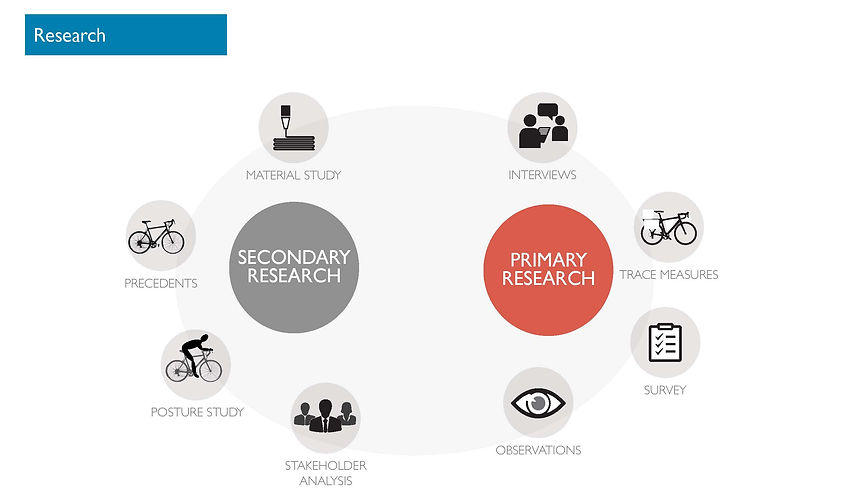

Understanding stakeholders
![]() | ![]() |
---|---|
![]() | ![]() |
![]() |
Numerous Interviews, Observations and Brainstorming
After many research, Fit occurred most frequently among all the raised issues

Looking at different bikes and thinking about the FIT issue, one idea came to our mind, what if we can make one bike fits every occasion. In which way, user will get most fit out of different ride purpose.
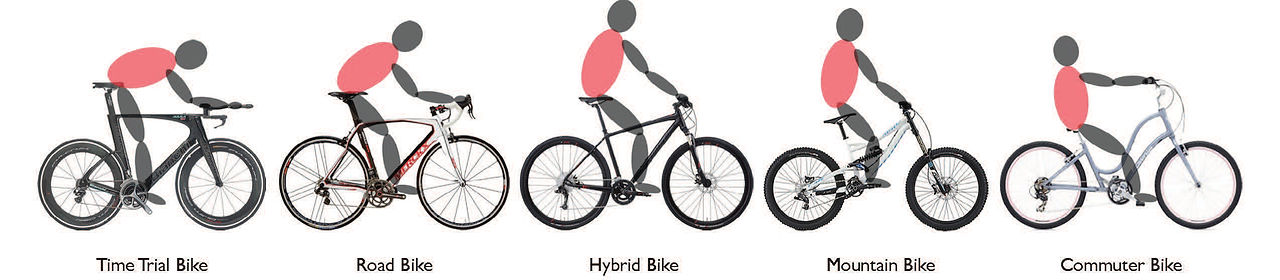
Some early ideas playing with bike frame geometry


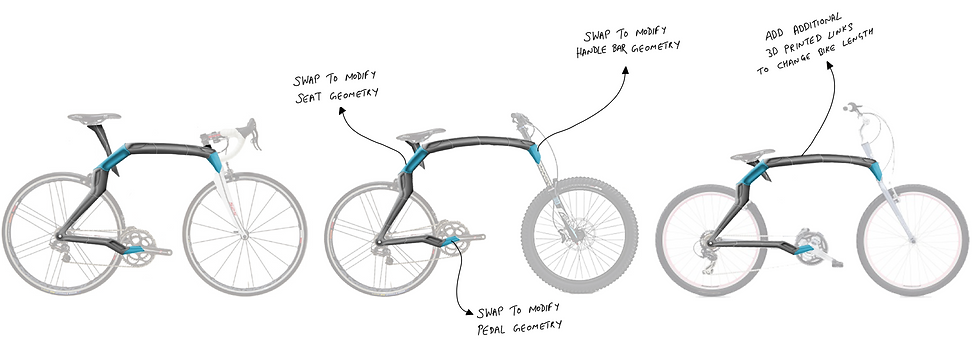
After all this brainstorming, we took a step back from all the fancy ideas, and started thinking on how to leverage 3D printing.
Finally, we decided to play bold, build a fully 3D printed Modular bike frame
​
By swapping key joints ( Head Tube, Seat Joint, Bottom Bracket ), user will be able to alter geometry of the bike frame to meet different riding needs.
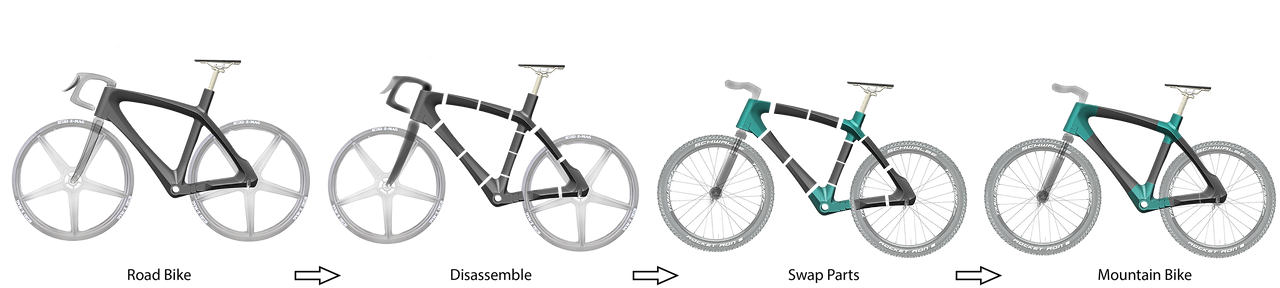
Material Testing
Different material thickness was tested prior to bike printing.
We are striving for highest strength at least weight (least material consumption, least build time and least cost).
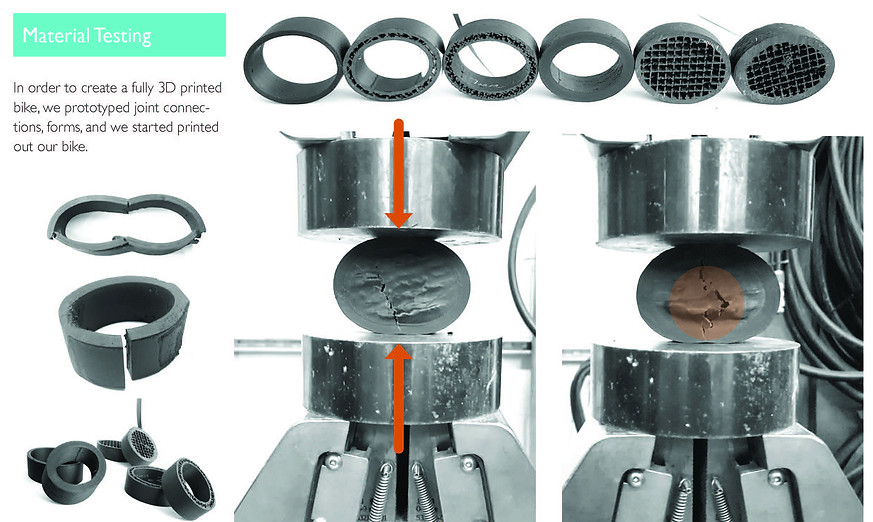
Compression force (Pound)

5mm wall thickness Horizontal compression
7mm wall thickness Horizontal compression
Deformation (Inch)
Results were promising with 5mm wall thickness and 7mm wall thickness samples withstanding over 800 pounds of compression within 0.2 inch of deformation.
​
We finally decided to use 5mm shell with internal web for our bike frame for its lighter weight with acceptable performance.
Design
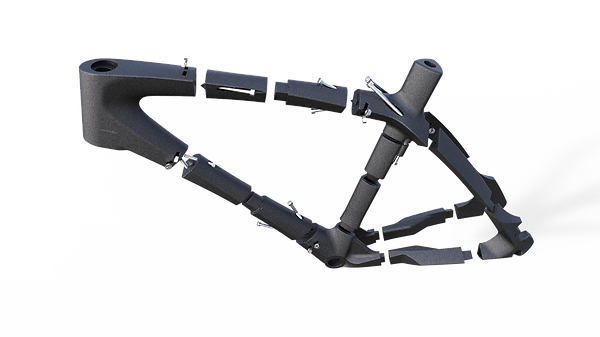
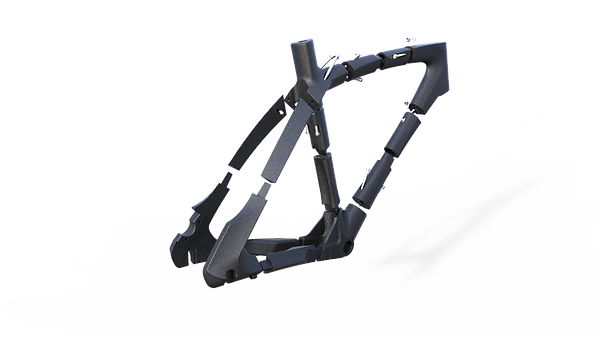

The modular bike frame will be joined together by screws and nuts. But screws and nuts only applies to replaceable parts (head tube, seat joint and bottom bracket).
The rest of the tubes are nested with each other and bonded with epoxy, since they will remain intact regardless of the bike genre.
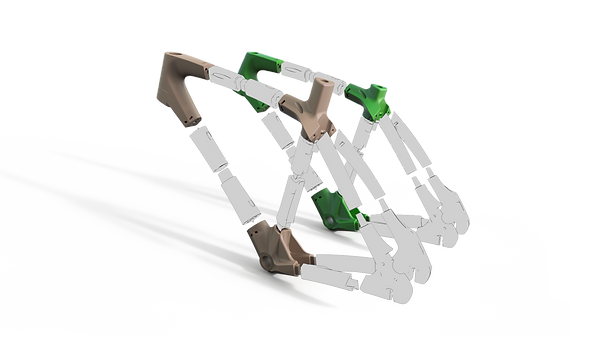
Different sets of replaceable joints will determine the geometry of the bike frame, in which way, MODU bike can be a road bike as well as a mountain bike.


Printing takes huge amount of time and effort, unfortunately, due to unexpected printer failure, we weren't able to finish all the printing by the end of spring 2016.

Based on force analysis, the upper half of the frame endures compression, while the lower half withstands tension, when holding human weight. So printing orientation was taken into consideration to deal with these two. For the parts endures more tension, the printing layer will better be parallel to tension force, whereas for compression, the layers are perpendicular to the compression force.
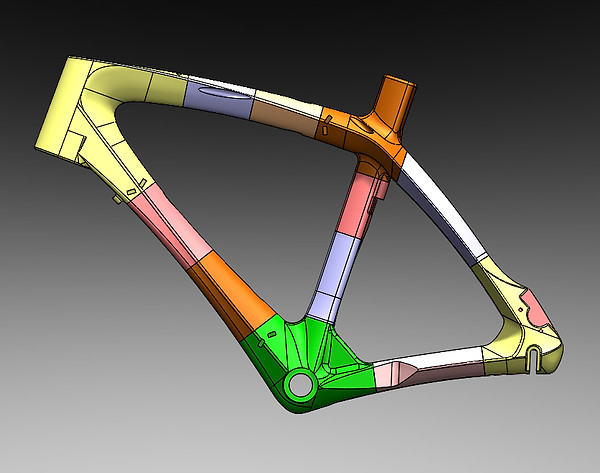
With every good print, there are a couple of bad ones. But when prints come out right, they
look beautiful. By the end of the spring, we are 3 prints away form having a prototype.

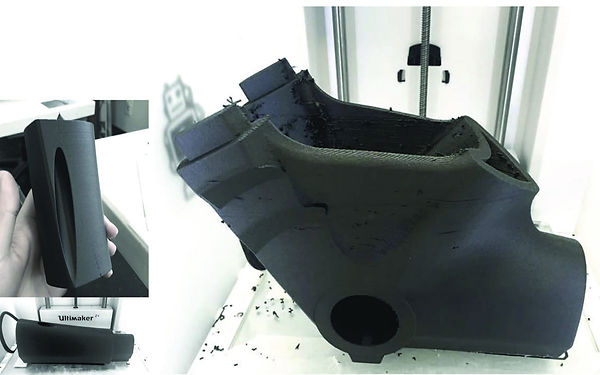
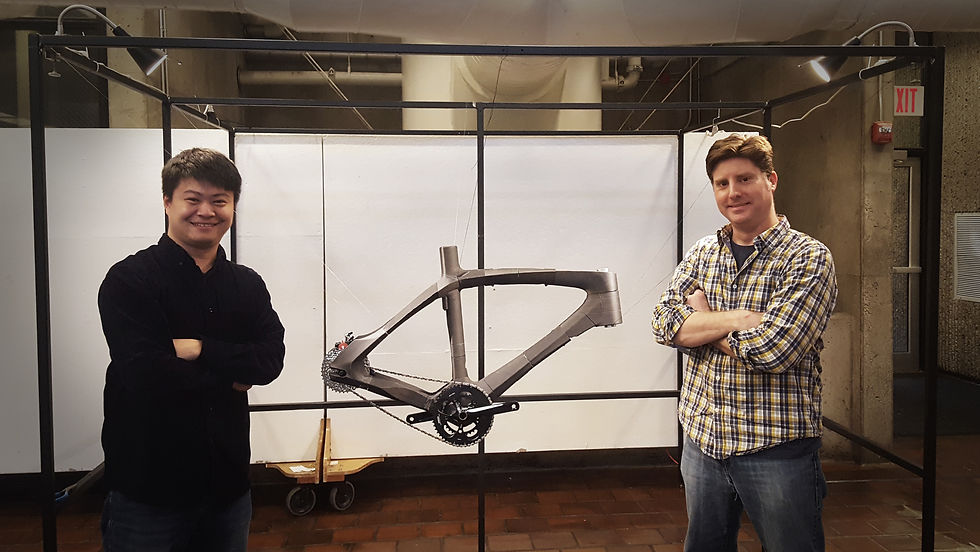
Bike Frame on ID's end of the year show. --- with Prof. Kevin Shankwiler